Hi Greg:
I was recently taught an easy method of fixing cam bearings that are tight because the 426 Hemi I'm building had tight bearings...I don't have a picture to show of the finished unit, but think I can describe the process...
The machinist I use builds the fastest qtr mile, twin turbo, nitrous, Toyota engines anywhere. Over 240 MPH out of V6 engines. Anyway, the cam bearings were tight in the Hemi, So he ask for the old Hyd cam core(we switched to a roller), then he took a cutoff wheel and cut a groove across the cam journals at an angle to the journal, and at a slight undercut to create a cutting edge, and a slight outward taper on the other side. He did this to each journal in just a few minutes. Then he slid in the cam and used a wrench to rotate around a few times, and viola, nice free turning and the bearings looked fine afterward.
Of course, I don't think this would be wise on an assembled engine, unless you could figure a way to clear the shavings.
Here is an image I made in an attempt to describe what I mean.
Here is a quick cad drawing describing the approximate cross section to cut into the journal. These are not critical angles or depths, it's done free hand, and if you screw up, just cut a little deeper or wider until you have a fairly sharp edge on the cutting side.
Again, this does not need to be precision in any way other than achieving a sharp edge on the left(counter clockwise) side of the journal surface.
When I purchased my Pontiac SD455 back in the mid 80's, I ran it for many years after installing a new Comp cam, running mid 12.40's with 7.5:1 compression and 87 octane fuel. However, after 40k miles or so I wanted to build more power. So I built the engine(at the time myself, I had access to a friends race machine shop for personal use). Long story short, I finish laying the crank, installing #1 piston with no rings to degree the cam, then go to install my new roller cam. While sliding the cam into place, everything was normal, get to the last(front) journal, and it won't even try to go in...
I start measuring, and we find the front cam bearing bore is .014" offset. How this can happen during manufacturing I can't fathom, without seeing how the cam bores are machined and how the tools are held.
I go to the recycle bin and there are my original bearings...my buddy who owns the shop and I start looking them over, and the carving knife marks are obvious on the first bearing. The factory didn't want to junk this low volume, high value block, and just carved the bearing material away.
I've come to find out, this wasn't an uncommon practice once you look at the total volume of engine production, you will have issues here and there, and certain of them were considered repairable. If it makes it through warranty...
End of the story is I had to wait 6 months for a specialty machine shop to line bore the cam journals, and charge me too much money to not follow my instructions. What I got back is not what I wanted, but looked like it would work. 40K more miles running in the mid 11's on street tires at 118mph, it spun the front cam bearing repair at 600 miles into a road trip to Hot August Nights in Reno. I noticed the oil pressure was 15psi lower than normal, but everything seemed to be running fine. Oil smelled and looked good, oil temp and water temp were normal...I thought it was a stuck oil pump bypass checkball or something. So kept driving to Reno another 300 miles. A nice shop in town let me pull my Canton inspectable filter and take a look...
Not pretty, I knew exactly what had happened when I saw the material. The machine shop had simply machined some aluminum into a front cam bearing, then press fit it with lock tight, and peened a few locations around it. It spun, wobbled back to the first cam lobe, and then was milled away on the drive to Reno. I knew this because it was only aluminum in the filter, no magnetic material, and the engine was still running well.
As a true hot rodder, I new that in a Pontiac, the very last thing to get oiled in the engine was the front cam bearing, so I wasn't to worried about debri contamination, and I have my filter bypass capped, so never unfiltered oil. I called a buddy and warned him he might have to drive south and trailer me at a moments notice, but I drove it another 900 miles home. Pulled the engine, and other than the cam bearing and minor bearing wear from thousands of full throttle passes on the street and strip, the engine was in fantastic shape.
That same roller cam is in the destroked 455 in my car now and running in the 10's. For anyone who cares, its almost the same cam specs as the FT cam for my slant. 254/260 @ .050" 286/292 @ lash(.017") installed at 102 in the SD, but 106 in the 446" because it's 11.2:1 compression.
Didn't mean to hi-jack the thread, but thought you and others might find this a good work around for cam bearings when building a motor.
I've been following your progress for years, and have torn down my 64 Valiant to follow almost the same track you have...especially like the trunk battery box. Putting the 5spd and new motor with external oil pump into the car this spring.
I've been preparing pictures for posting about my build soon.
Gearhead
AKA Karl
_________________
64 GTO...10.80's@122 on street radials
Destroked 455, Qjet, stock ign, 2400 stall
64 Valiant
Old 225, 4spd, 2.92-8.75, 2bbl, headers
dual 2.25"
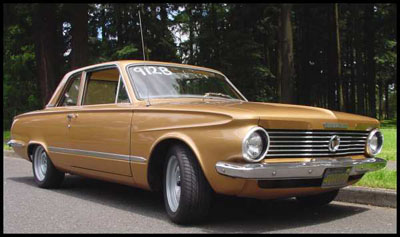